Home » Trailer Industry » Misc Information » Bendix Remanufactured Components & Global Reman Day
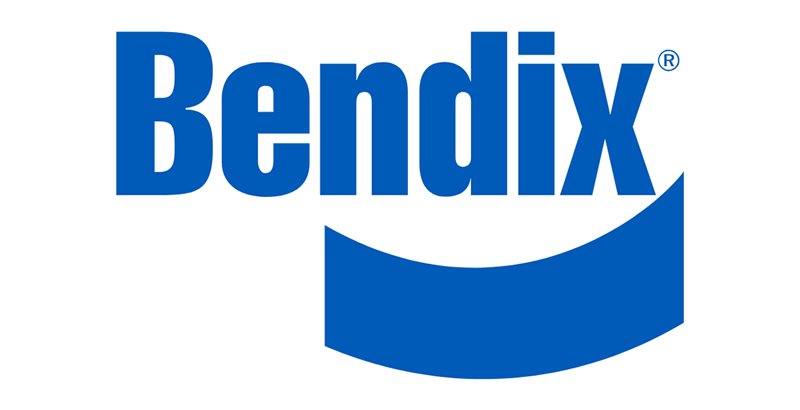
REMANUFACTURING MAKES A DIFFERENCE AT BENDIX – AND BEYOND
Company Marks Global Reman Day 2020; Remanufactured 2.7 Million Components Last Year
ELYRIA, Ohio – (Trailer Technician) – Last year, Bendix Commercial Vehicle Systems produced 2.7 million remanufactured components, saving more than 6,900 tons of raw materials and reducing its carbon footprint by more than 24,000 equivalent tons of CO2. From 2017 to 2019 – the years preceding each of the three annual Global Remanufacturing Days to date – those total numbers are now 7.2 million parts, more than 20,300 tons of materials saved, and more than 71,000 equivalent tons of CO2.
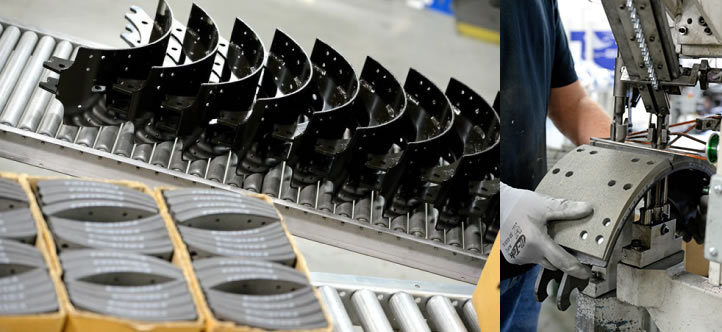
“Of course, we’ve been remanufacturing for over 40 years now, so the impact is really far greater,” said Maria Gutierrez, director of corporate responsibility and sustainability. “Celebrating Global Reman Day may be relatively new, but remanufacturing has been a key part of Bendix’s operations and sustainability commitment for more than a generation.”
Global Reman Day, an initiative of the Remanufacturing Industries Council, is an occasion to advance the remanufacturing industry through remanufacturer-hosted events and workforce development programs. Launched in 2018, it will be marked this year on April 9. Remanufacturers will offer webinars and other online resources to raise awareness of remanufacturing’s benefits around the world.
Bendix is the North American leader in the development and manufacture of active safety, air management, and braking solutions for commercial vehicles. The company remanufactures foundation drum brake shoes, valves, air dryers, compressors, steering gears, and electronics.
Bendix’s remanufacturing strategy continues to be guided by its focus on people, the planet, and profit, as the company aims for sustainable long-term growth paired with consistent reduction of its environmental impact.
“Through a reduction of raw materials usage, energy conservation, and elimination of certain waste sent to landfills, remanufacturing aligns with Bendix’s commitment to the United Nations’ Sustainable Development Goal 12 (SDG 12) – Responsible Consumption and Production,” Gutierrez said. “Additionally, because we’re extending the lifetime of previously produced components, reman creates value and contributes to the circular economy, while also cutting down the use of new metal materials and the carbon dioxide impact of producing them.”
Rebuilding Doesn’t Equal Remanufacturing
Global Reman Day 2020 is a good chance to reemphasize what sets remanufacturing apart from rebuilding – because the terms aren’t interchangeable, noted Henry Foxx, Bendix director of remanufactured products.
“A genuine remanufactured component has to be rebuilt by the original equipment manufacturer – an OEM, such as Bendix – using a mix of reconditioned components and brand-new components from the very same suppliers the OEM uses for original equipment,” Foxx explained. “Components such as gaskets and bushings, which exhibit high levels of wear during normal operation, must be replaced with original spec components identical to the ones you’d find on a brand-new product.”
Rebuilt parts – often offered as a lower-cost alternative to remanufactured parts – don’t have to meet those stringent requirements. A rebuilt air compressor, for instance, may simply be cleaned or repainted, with wear parts that are reused or replaced with inferior versions. Rebuilt brake shoes may just be relined with new friction, and not coined to return them to the proper OEM geometry, which can affect performance and brake life.
“OEM-level remanufacturers like Bendix are also able to conduct the same post-production testing as performed on OEM components to ensure proper performance levels,” Foxx said. “Ultimately, genuine remanufactured components deliver reduced replacement costs and extend vehicle life, reducing total cost of ownership (TCO), and helping fleets and owner-operators manage their bottom line. And at Bendix, they’re one more way we’re working with our customers to shape tomorrow’s transportation together, improving uptime and keeping vehicles on the road and in safe operating condition.”
Learn more about Bendix remanufactured brake shoes at www.safertrucks.com/shoes, and find further insight on remanufacturing and replacement parts at the Knowledge Dock® (knowledge-dock.com), which features videos, blog posts, podcasts, and white papers, as well as an archive of the Bendix Tech Tips series.
About Bendix Commercial Vehicle Systems LLC
Bendix Commercial Vehicle Systems, a member of the Knorr-Bremse Group, develops and supplies leading-edge active safety technologies, energy management solutions, and air brake charging and control systems and components under the Bendix® brand name for medium- and heavy-duty trucks, tractors, trailers, buses, and other commercial vehicles throughout North America. An industry pioneer, employing more than 3,400 people, Bendix is driven to deliver solutions for improved vehicle safety, performance, and overall operating cost. Contact us at
1-800-AIR-BRAKE (1-800-247-2725) or visit bendix.com. Stay connected and informed through Bendix expert podcasts, blog posts, videos, and other resources at knowledge-dock.com. Follow Bendix on Twitter at twitter.com/Bendix_CVS. Log on and learn from the Bendix experts at brake-school.com. And to learn more about career opportunities at Bendix, visit bendix.com/careers.